Force feedback is a new technology that serves a great deal of help in human-machine interfaces. For example during tele-operation of a robot used in a minimally invasive robotic surgery, current available technology only gives visual feedback to the surgeon. Hence the surgeon will not be able to feel the environment through which the end-effector of the robot navigates. Thus providing force feedback here will help the surgeon guide the end-effector of the robot exactly along the path that he intends to with the aid of visual and force-feedback technology. To achieve this we need an easily controllable actuator at the user's end that gives quick response. MR actuators that are appropriately designed can be used here easily. The MR actuator used here must have low force levels since its being operated by a human hand. Hence shear mode configuration is best suited for this application. MR sponge dampers that are gaining popularity by the day that operate in shear mode can be used here.
The advantages of MR sponge dampers are no requirement of seals, lesser volume of MR fluid, and flexibility in multi dimensional movement, etc. The MR sponge damper consists of a polyurethane foam soaked and saturated in MR fluid and wound around the electromagnet-cum-piston. This piston with the foam slides to and fro inside an outer cylinder. By controlling the current through the electromagnet we can control the force across the MR damper and this can be used as a force-feedback device. The proposed force-feedback experiment includes a simple setup that depicts a typical situation wherein a user controls the movement of an external linear hydraulic actuator using the MR sponge damper. A force and a displacement sensor sense the environment conditions along which the end effector of the hydraulic actuator moves. This information is then used to control the current through the electromagnet and hence provide appropriate force feedback to the user. The damper and the proposed setup figures are shown below. The damper schematic, the actual fabricated damper and the setup are shown in the following figures.
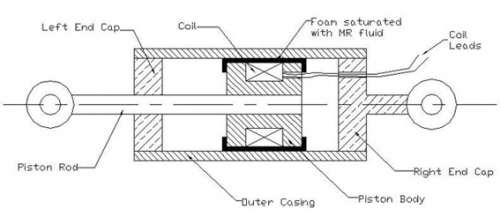
Fig 4 Schematic of MR sponge damper
![]() |
|
Figs 5 & 6 MR sponge force-feedback device and MR foam
Fig 7 Schematic of the Force Feedback Setup
Fig 8 A view of the one dimensional force feedback system
Fig 9 Experimental results